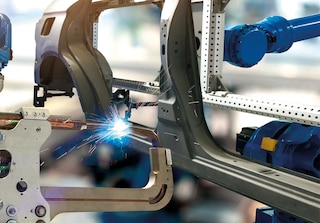
MRP: un hito para el proceso de producción
La planificación de material para el proceso de producción supone todo un complejo desafío logístico para cualquier instalación. Qué cantidad de materia prima requiero, cuándo la necesito o qué número de unidades hay que producir son algunas de las preguntas a las que, desde hace décadas, los fabricantes dan respuesta gracias a la ayuda del sistema MRP (Material Requirements Planning).
En este post analizaremos todo lo que envuelve a la planificación de requerimientos de materiales: que és, cómo funciona, sus ventajas y por qué ha sido y es tan importante en el proceso de producción. Además, explicaremos la diferencia entre un sistema MRP y un ERP.
¿Qué es un MRP?
La planificación de requerimientos de materiales o Material Requirements Planning es un sistema diseñado para gestionar los procesos de producción y coordinar con antelación las actividades de fabricación, compra y entrega del producto elaborado.
El sistema MRP irrumpió con fuerza en la década de los 70 y su crecimiento fue meteórico. Según el libro Production Planning and Control: A Comprehensive Approach, escrito por D.R. Kiran en 1975, se estima que ya 700 empresas utilizaban el sistema MRP para optimizar sus procesos de producción. Dicha cifra fue aumentando un 174% anual, hasta alcanzar las 8.000 compañías en 1981, tan solo seis años después.
Hoy en día, el sistema MRP es considerado el origen de los actuales programas informáticos orientados a la mejora de los procesos industriales: MRP II (Manufacturing Resource Planning), ERP (Enterprise Resource Planning), CRM (Customer Relationship Management), SRM (Supplier Relationship Management) o MES (Manufacturing Execution System).
El MRP organiza las actividades de fabricación y optimiza la gestión del stock en función de las necesidades de la empresa. Con la ayuda del Material Requirements Planning, cualquier fabricante está más cerca de lograr su principal objetivo: disponer en todo momento del material exacto para producir los productos y entregarlos a los clientes en el menor tiempo y al menor costo posible.
¿Cómo funciona un MRP?
El sistema MRP precisa de unos datos de entrada que son indispensables:
- Plan maestro de producción: conocido como MPS (Master Production Schedule), evidencia cuántos artículos serán producidos y en qué períodos de tiempo.
- Lista de materiales: el BOM (bill of materials) especifica qué materias primas, en qué cantidad y los procesos de producción necesarios para obtener una unidad de producto final.
- Registro de inventario: detalla la información relacionada con el stock (inventario disponible, stock bajo pedido, pedidos cancelados, tiempo de espera, etc.). La finalidad es saber qué materia prima está disponible para su uso inmediato.
Con todos estos datos de entrada en la mano, el sistema de planificación de requerimientos de material ofrece los siguientes datos de salida:
- Plan maestro de producción recomendado: elabora un calendario con las fechas relacionadas con el proceso de producción (inicio y finalización), las cantidades para cada paso de la hoja de ruta y la lista de materiales (BOM). Todo ello buscando satisfacer la demanda especificada en el plan maestro de producción.
- Programa de compras recomendado: muestra las fechas en las que se recibirán los materiales comprados, así como las fechas en las que deben originarse los nuevos pedidos para que coincidan con el plan de producción.
De ese modo, el sistema MRP nos asegura que recibiremos los materiales adecuados a fin de mantener un nivel mínimo de inventario para abastecer la producción y, al mismo tiempo, una planificación eficiente de las actividades de fabricación, compra y entrega del material.
Ejemplo de planificación de los requerimientos de materiales
Tras realizar el plan maestro de producción y la lista de materiales, se determina que para fabricar un producto final (producto X) se necesitan 2 unidades del material A y 1 unidad del material B. Por cada unidad del material A se necesitan 3 unidades de la pieza C y por cada unidad del material B se requieren 2 unidades de la pieza C y 4 unidades de la pieza D.
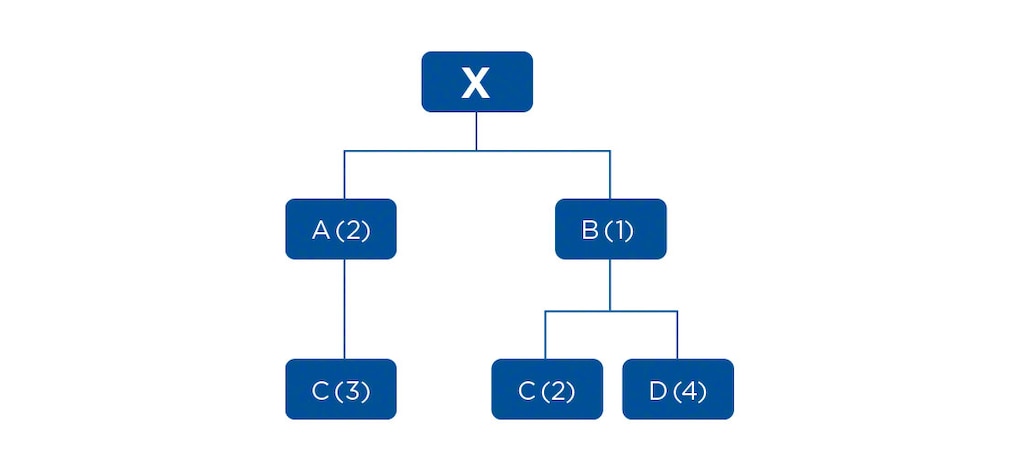
Posteriormente, detallamos el registro de inventario (IRF, Inventory Record File), que refleja el inventario disponible y el tiempo de espera (lead time) que se tardará en recibir cada producto:

Así queda resumida la planificación de requerimientos de materiales en el supuesto de que tengamos que producir 100 unidades del producto X en 10 semanas:
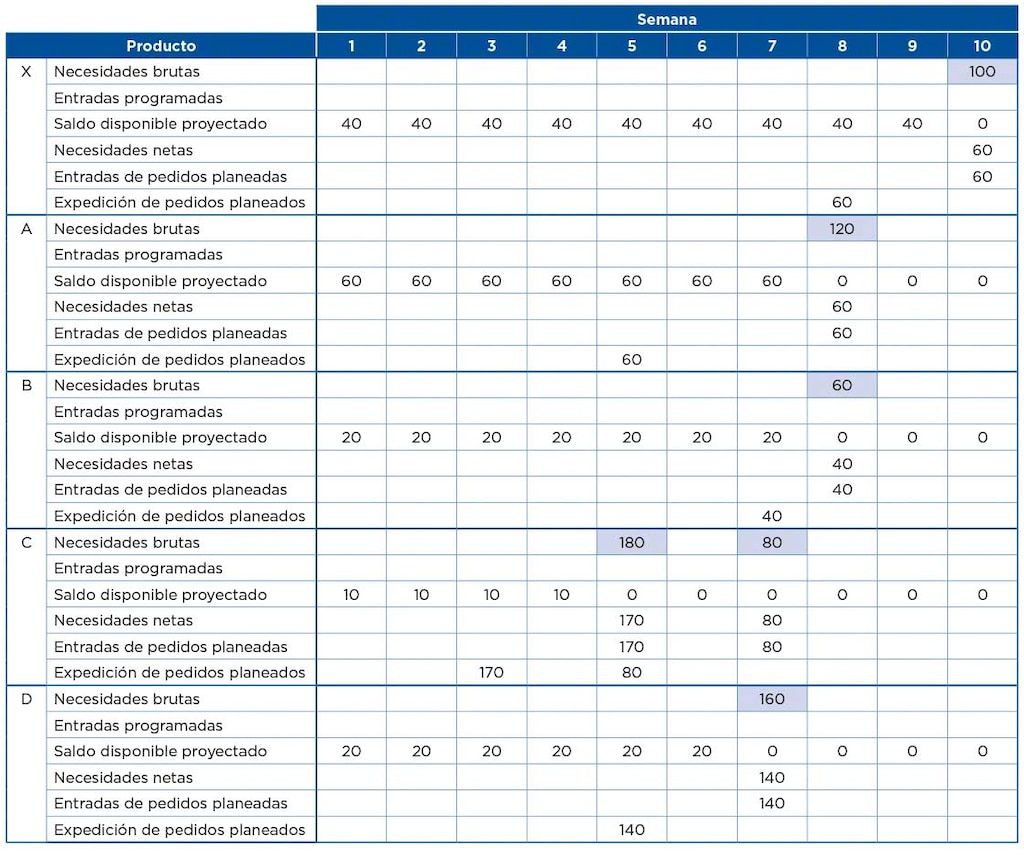
La tabla refleja que, para disponer de 100 unidades del producto X en la semana 10, se necesitan 60 unidades adicionales que se sumarán a las 40 unidades que ya están disponibles en el inventario. Dado que en el Registro de inventario hemos definido que el tiempo de espera (lead time) para el producto X es de 2 semanas, el pedido se deberá realizar en la semana 8.
Si por cada unidad del producto X se precisan 2 unidades del producto A, significa que para la semana 8 se requerirán 120 unidades del producto A. Como que en el inventario ya se dispone de 60 unidades, la necesidad neta del producto A también será de 60 unidades. Teniendo en cuenta el tiempo de espera, dichas unidades se tendrán que solicitar con tres semanas de antelación.
Siguiendo el mismo procedimiento, se establecen las necesidades netas del producto B, C,. D y F, así como la semana en la que deben ser solicitados.
Funciones y ventajas de utilizar un MRP
Dentro de un proceso de producción, la planificación de requerimientos de materiales tiene la función de calcular la materia prima necesaria, los componentes requeridos y la cantidad de producto terminado que se fabricará.
La planificación de requerimientos de materiales proporciona los siguientes beneficios:
- Disponibilidad total de la materia prima para la producción.
- Cumplimiento de los plazos de entrega.
- Mantenimiento de un nivel de inventario bajo, tanto de materia prima como de producto terminado.
- Planificación de actividades de fabricación, órdenes de entrega y compras.
- Reducción de costos.
El sistema MRP soluciona muchos de los problemas con los que se encuentran a diario los fabricantes, especialmente en la compra de materia prima. Una compra incorrecta o insuficiente puede demorar los plazos de entrega y, en el caso de comprar más material del necesario, supone un sobrecosto de almacenaje.
Diferencias entre MRP y MRP2
A principios de la década de los 80, el sistema MRP (Material Requirements Planning) evolucionó al MRP2 (Manufacturing Resource Planning), un sistema de planificación más avanzado y con un alcance más amplio. A grandes rasgos, las principales diferencias entre ambos sistemas son:
- Además de planificar la gestión de los materiales requeridos para la producción, el MRP2 integra otros departamentos de la compañía, como el comercial, financiero, etc.
- Mientras que el MRP trabaja en función del plan maestro de producción, el MRP2 se basa en el estudio de la demanda y del mercado.
- El MRP2 analiza el comportamiento de la empresa para ejecutar una planificación eficiente, mientras que el MRP lo hace a través de la práctica y la experiencia previa de la empresa.
- El MRP es un sistema abierto al revés que el MRP2, que es cerrado. Eso quiere decir que el MRP2 tiene la capacidad de retroalimentarse con los informes que genera, pudiendo hacer replanificaciones más ajustadas a la realidad.
El MRP2 es la versión modernizada del MRP. Además de responder a la pregunta cuánto y cuándo hay que producir, también define qué recursos, en qué cantidad y en qué momento serán necesarios para llevar a cabo dicha producción.
Diferencias entre MRP y ERP
El sistema ERP (Enterprise Resource Planning) se utilizó por primera vez en la década de 1990 y es, aun si cabe, más completo y polivalente que sus antecesores sistemas MRP. Si por algo se caracteriza y lo hace diferente a los MRP es porque posee la capacidad de centralizar en un mismo sistema todas las áreas de la empresa.
Dicho de otra manera, el MRP es un software que trabaja en solitario, mientras que el ERP integra y combina los sistemas informáticos que emplea cada departamento a fin de crear una base de datos centralizada. De esa forma, cualquier área de la compañía puede acceder a la información en tiempo real, controlar flujos de trabajo, minimizar errores y comunicarse con otros departamentos.
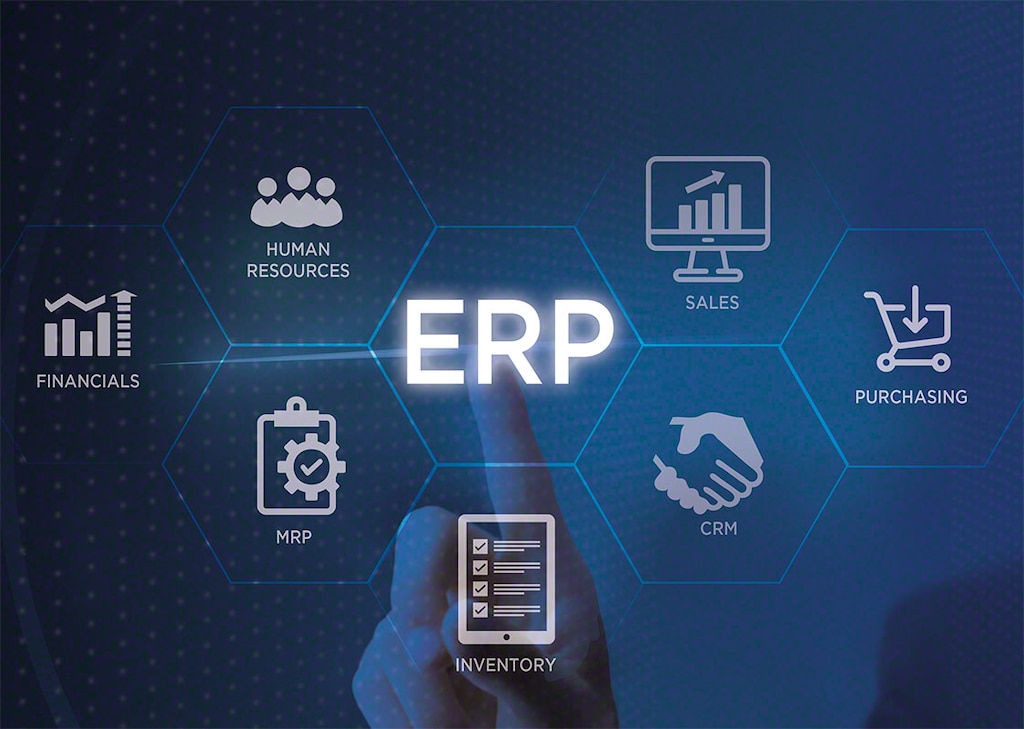
MRP: en la estela de los avances tecnológicos
Después de cincuenta años funcionando, es justo aseverar que la planificación de requerimientos de materiales ha marcado un antes y un después en el proceso productivo. Su esencia, que no es otra que anticiparse a las necesidades para poder planificar, se ha adaptado a las nuevas tecnologías con vistas a potenciar la rentabilidad de la cadena de suministro.
En Mecalux siempre apostamos por las soluciones tecnológicas más innovadoras del mercado, tanto de almacenaje como de gestión logística, como es el caso de Easy WMS. Este sistema se puede integrar con cualquier ERP para que ambos sistemas se transfieran datos e información destinada a lograr una mayor productividad en el almacén.
Contacta con nosotros si quieres que un equipo de especialistas te ayude a sacar un mayor partido a tu cadena de suministro.