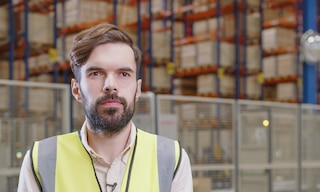
Entrevista a Pavol Masarovič, director de Operaciones de IKEA Components Eslovaquia
“La automatización del almacén se completó sin detener su funcionamiento”
Sobre IKEA Components
IKEA Components, filial de la multinacional sueca IKEA encargada del empaque y entrega de accesorios y componentes para muebles, ha automatizado con transelevadores trilaterales su almacén de Malacky (Eslovaquia) sin detener su actividad en ningún momento. Además, ha implementado el sistema de gestión de almacenes Easy WMS para aumentar su eficiencia.
Mecalux entrevista a Pavol Masarovič, director de Operaciones de IKEA Components Eslovaquia. La filial ha automatizado su almacén de Malacky (Polonia) sin dejar de trabajar en su interior en ningún momento y, además, ha aumentado su capacidad de atender pedidos.
-
IKEA tiene presencia en 62 mercados y posee más de 450 tiendas. ¿Cómo era la logística de IKEA Components antes de su automatización?
Hasta entonces toda nuestra área de envíos funcionaba de forma completamente convencional. Es decir, todos los movimientos y traslados de tarimas se hacían con montacargas o en racks de pasillo estrecho. Llevábamos las tarimas desde el área de producción y las guardábamos en el almacén. Este sistema de trabajo requería más tiempo, más equipamiento para el manejo de materiales y más compañeros ocupados haciendo las mismas tareas, por lo que decidimos automatizar algunos aspectos.
-
Mecalux automatizó el almacén de IKEA Components en Malacky sin interrumpir su operación. ¿Cómo se desarrolló este proyecto?
El principal requisito que planteamos a Mecalux fue preparar y diseñar todo el proceso de manera que no influyera en el funcionamiento del almacén durante su instalación. Fue algo que pedimos incluso antes de comenzar. No cabía la posibilidad de cerrar el recinto por completo.
El proyecto se dividió en cuatro fases. En cada una se instalaron tres transelevadores trilaterales y se extendió el circuito de transportadores. Al dividir la intervención en distintas etapas, logramos completarla afectando únicamente al 25% de la capacidad total durante cada fase. Por lo tanto, el impacto de estos trabajos fue menor y no influyó en nuestra actividad diaria.
Ahora nos centramos en mantener el stock mientras la automatización se encarga de trasladar las tarimas
-
¿Qué ventajas ha aportado el almacén automatizado a IKEA Components?
Nos da más flexibilidad y eficiencia, empezando desde los movimientos de las tarimas. Antes estábamos obligados a hacerlo todo manualmente, pero hoy en día no nos preocupamos de los traslados de mercancía porque la automatización lo hace por nosotros. Así, podemos centrarnos en mantener el stock. Tener los productos en un almacén automatizado nos aporta una mejor visibilidad del inventario y, además, es más difícil cometer errores que con una gestión convencional.
El sistema es fácil de controlar porque se maneja con el sistema de gestión de almacenes Easy WMS. El programa controla todos los procesos y, cuando necesitamos hacer llegar las tarimas a nuestros clientes, envía las instrucciones. A continuación, las tarimas dejan el almacén de modo autónomo.
Hemos podido comprobar los beneficios de los sistemas de almacenamiento automatizados, en especial durante el periodo de pandemia. Tuvimos algunos compañeros de baja por enfermedad pero, al contar con un almacén que no dependía tanto de los operadores, pudimos seguir atendiendo las demandas de nuestros clientes y enviar todas las tarimas que nos solicitaban.
-
¿Qué ruta hace una tarima desde que accede hasta que abandona la instalación?
Completamos la instalación afectando únicamente al 25% de la capacidad total durante cuatro fases Todas las tarimas que llegan al almacén de distribución provienen de nuestra zona de producción. Los vehículos de guiado automático se encargan de traerlas desde nuestra línea de cierre de tarimas. Luego, siguen su camino por la cinta transportadora y entran en el puesto de inspección de entrada (PIE) instalado por Mecalux. Allí Easy WMS elige la ubicación de la mercancía y ordena la tarea de trasladar la tarima automáticamente a uno de los doce pasillos de almacenamiento. Después, cuando la tarima es requerida en algún lugar y necesitamos enviarla a algún cliente, todo el proceso arranca de forma robotizada en cuanto un operador da la orden. Entonces, las tarimas salen por una u otra cinta transportadora en función de su destino final y van a las distintas zonas de carga por el camino más corto posible.
-
¿Qué balance hace de esta transformación intralogística?
El de Malacky fue un proyecto que duró casi tres años y en el que nos enfrentamos a varios retos, pero conseguimos resolverlos todos de modo muy profesional y sin apartarnos del objetivo de mejorar nuestra eficiencia. La cooperación con Mecalux fue muy profesional, las relaciones muy cordiales y al final completamos la tarea con total éxito. Hubo muchas personas involucradas, tanto por su parte como por la nuestra. En resumen, fue un proyecto formidable para todos nosotros en el que todos aprendimos algo nuevo y ganamos habilidades y experiencias que podremos aplicar en el futuro.